Д.А. Самосий
Ежегодно мировой горнодобывающей промышленностью перерабатываются миллионы тонн руды и минерального сырья, более 95 % которых впоследствии складируется в виде отвалов пустой породы и хвостов обогащения.
Постоянно возрастающий спрос на металлы в сочетании с истощением запасов высококачественных первичных руд приводит к тому, что техногенные минеральные образования (ТМО) – хвосты обогащения прошлых лет отработки с относительно высокими содержаниями железа, меди, никеля, цинка, а также золота и серебра начинают представлять все больший интерес.
Поскольку хвосты находятся на поверхности и в большинстве случаев они уже измельчены, затраты на извлечение из них остаточных металлов часто экономически более привлекательны, чем разработка глубокозалегающих рудных тел или песков. Кроме того, они могут содержать металлы, доизвлечение которых ранее, при первоначальной переработке минерального сырья, не считалось целесообразным, но на сегодня их ценность и потребность в них выросли.
Цены на некоторые металлы за последние 5 лет [1]
Для переработки золотосодержащих ТМО применяются те же методы, что и для рудного сырья, большая часть которого перерабатывается с применением гидрометаллургических, а также флотационных и гравитационных методов обогащения, в том числе и их сочетаний. Каждый из этих методов имеет свои преимущества и недостатки. Гидрометаллургия, к примеру, обеспечивает максимальное извлечение, но при этом требует наиболее высоких капитальных и эксплуатационных затрат. Гравитационное обогащение, напротив, как правило, наиболее доступное решение с минимумом капитальных и эксплуатационных затрат, однако и минимальной степенью извлечения по сравнению с гидрометаллургическими и флотационными методами.
Выбор применения той или иной технологии в первую очередь зависит от объемов техногенного минерального сырья и запасов золота, находящегося в нем. Запасы в 4-5 т золота и больше позволяют достаточно серьёзно рассматривать технологию гидрометаллургической переработки ТМО, особенно, если в районе имеются другие схожие по технологическим свойствам объекты.
Так, на базе 25 миллионов тонн золотосодержащих хвостов, накопившихся за более чем 80-ти летнюю деятельность ГМК «Казахалтын» (Казахстан), в 2017-2018 годах было построено три гидрометаллургических установки по переработке ТМО с применением технологии сорбционного выщелачивания:
- на ЗИФ «Жолымбет» с производительностью 2,25 млн. тонн хвостов в год;
- на ЗИФ «Аксу» – 2,25 млн. тонн хвостов в год;
- на ЗИФ «Бестобе» – 2,5 млн. тонн хвостов в год.
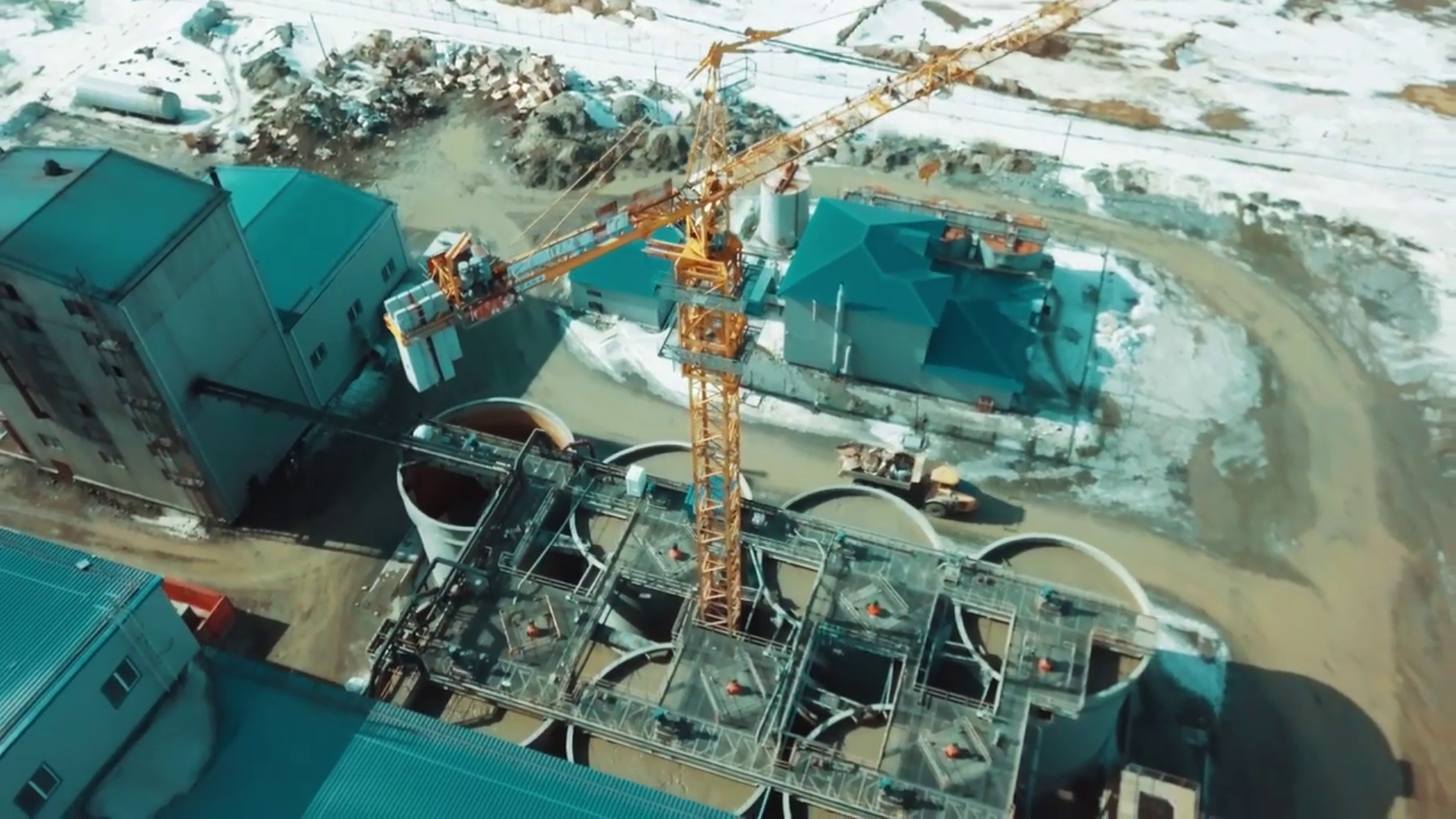
На установках «Жолымбет» и «Аксу» переработка хвостов осуществляется по полной технологической схеме с доизмельчением хвостов, сорбционным цианированием, десорбцией и получением сплава Доре в виде товарного продукта.
Схема установки Бестобе ограничена сорбцией выщелачиваемого золота на активированный уголь. Дальнейшая переработка насыщенного золотом угля осуществляется на ЗИФ «Аксу».
Технологический срок жизни проекта переработки лежалых хвостов рассчитан на 4-5 лет. В планах компании ГМК «Казахалтын» за это время получить из техногенного сырья 13,6 т золота [2]. По окончании переработки хвостов данные обогатительные установки будут переведены на переработку руды.
В отличии от гидрометаллургии технология гравитационного обогащения позволяет экономически эффективно отрабатывать не только крупные хвостохранилища содержащие десятки миллионов тонн материала, но также сверхмелкие объекты объем которых не превышает 0,5 млн. т – эфельные отвалы, спец.отвалы ШОФ и т.д.
Если отбросить промывочные приборы и установки, работающие на эфельных отвалах россыпной золотодобычи, число которых подсчитать не представляется возможным, то сравнительно небольшие гравитационные обогатительные установки, в том числе для проведения опытно-промышленных работ и изучения возможности переработки ТМО, сегодня работают на отходах кучного выщелачивания ЗИФ месторождения Мезек (Казахстан), на хвостохранилищах золотоизвлекательных фабрик: рудника Мгарт (Концерн «Мульти-групп»), ЗИФ-3 (ПАО «Высочайший», Иркутская область), рудника Джульетта (ООО «Северные прииски», Магаданская область), Рудника Ветренский (ООО “Электрум-плюс”, Магаданская область), месторождения Школьное (Магаданская область) и др.
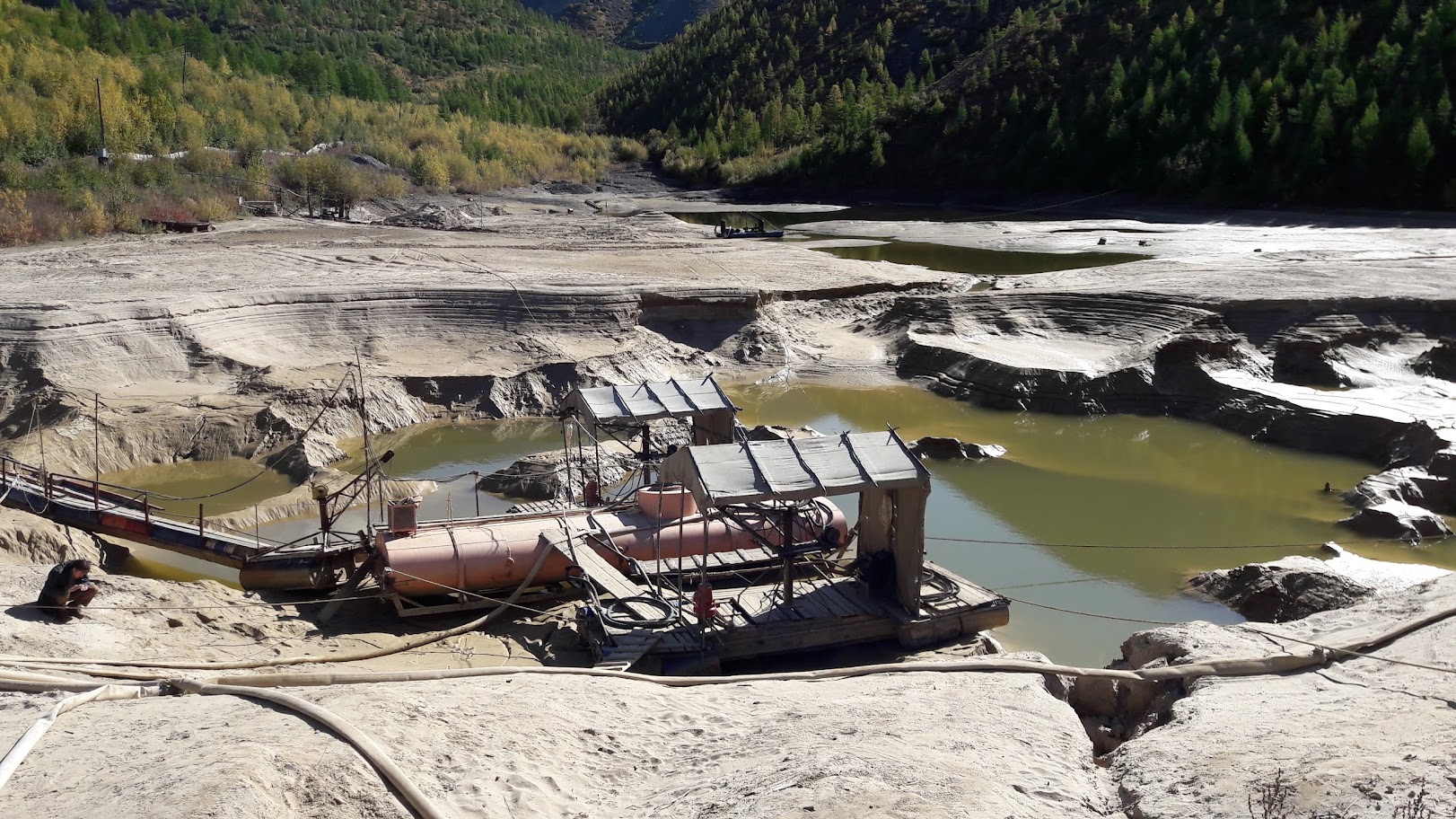
Товарным продуктом этих обогатительных установок является гравитационный концентрат, который в дальнейшем направляется для переработки либо на собственные установки выщелачивания, либо на медерафинировочные и аффинажные предприятия.
К примеру:
- Из 7,5 млн. т отходов кучного выщелачивания золота месторождения Мезек по самой простой технологии гравитационного обогащения отсева класса минус 2 мм при сезонной работе (8 месяцев в году) за 5 лет можно получить порядка 1,5 т золота в виде золотосодержащего концентрата качеством не менее 250 г/т.
- Переработка текущих хвостов рудника Ветренский позволяет ежегодно доизвлекать 15 кг золота в виде гравитационного концентрата с содержанием золота не менее 100-150 г/т, отправляемого на дальнейшую переработку в АО «Уралэлектромедь» (УГМК).
- Сезонная переработка лежалых хвостов рудника Джульетта при производительности 21,5 тыс. т хвостов в месяц позволяет дополнительно получить за рабочий сезон длительностью порядка пяти месяцев 125 кг золота (25 кг в месяц) [3].
- Предприятием, производившим разработку месторождения «Школьное», являлось ЗАО «Нелькобазолото», по отчетам которого, на момент окончания работ в 2008 году, спецхранилище рудника «Школьный» составляло более 300 тыс.т хвостов с общим количеством золота более 700 кг.
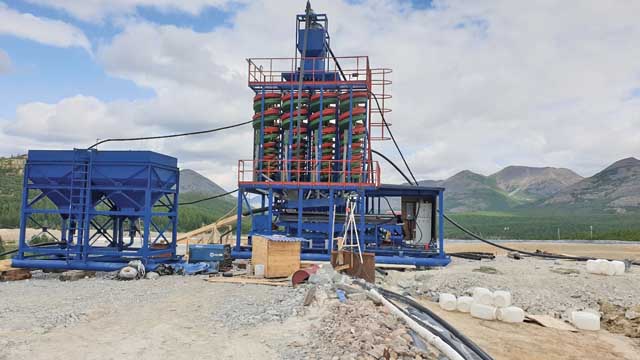
Технология обогатительных установок не ограничивается выбором только между гравитацией и гидрометаллургией, есть примеры различных сочетаний.
Гравитационно-флотационная технология переработки ТМО применяется на обогатительной установке «Нординвэс» для переработки лежалых хвостов хвостохранилища №1 и текущих хвостов Норильской обогатительной фабрики (НОФ). Переработка хвостов НОФ, с производительностью порядка 5 млн. тонн в год на этой установке осуществляется с 2004 года [4]. Товарным продуктом обогатительной установки является гравитационно-флотационный медно-никелевый концентрат (75 тыс. т ежегодно), содержащий также золото и металлы платиновой группы, поставляемый обратно на НОФ с целью последующего вовлечения его в оборот ГМК Норильский Никель.
содержание %, г/т | |||
не менее 25 г/т | |||
В среднем переработка лежалых и текущих золотосодержащих хвостов позволяет извлекать не менее 0,2-0,3 г золота с одной тонны материала, используя при этом только гравитационные методы обогащения. Применение цианирования позволяет поднять количество извлекаемого золота в 1,5-2,0 раза и обеспечить извлечение в среднем не менее 0,3-0,6 г золота с каждой переработанной тонны.
Анализ производственных результатов крупнейших производителей золота в России за 2020 год (АО «Полиметалл» [5] и ПАО «Полюс» [6]) показывает, что среднее количество извлекаемого золота находится на уровне 0,22 г на тонну горной массы.
Учитывая, что:
- количество золота, извлекаемого из руды с тонны горной массы, не превышает количество золота, извлекаемого с тонны ТМО;
- при переработке ТМО нет необходимости использовать в полном объеме наиболее энергозатратный технологический процесс – измельчение материала
вовлечение в отработку золотосодержащего техногенного сырья, особенно сформированного в прошлом столетии, представляет огромный экономический интерес.
Возможность вовлечения в переработку техногенного сырья не ограничивается только золотом. Так, наименее капиталоемкие гравитационные обогатительные установки эффективно работают при переработке лежалых хвостов ОФ Хинганолово (ООО «Ресурсы Малого Хингана»), шламохранилища дробильно-обогатительной фабрики № 5 (Магнитогорский Металлургический Комбинат), золошлаковых отходов Ангарской ТЭЦ (ПАО «Иркутскэнерго»), хвостов вольфрамовой ОФ рудника Бом-Горхон («Старательская артель «Кварц») и др.
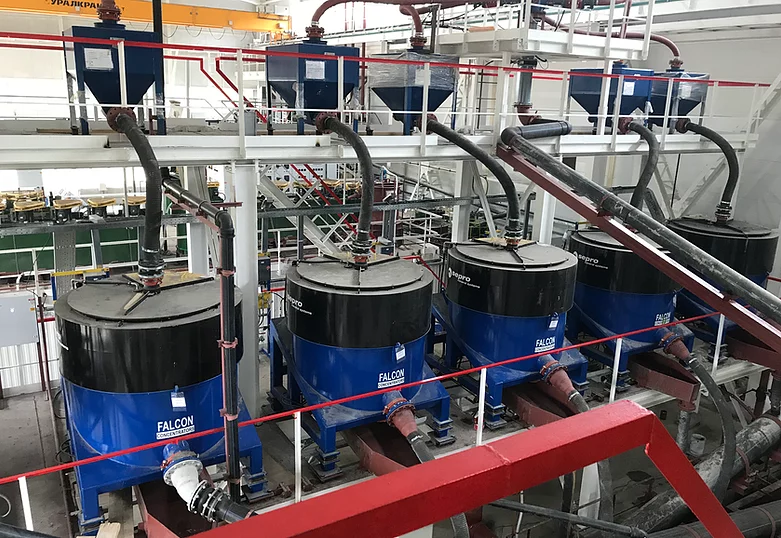
К примеру:
- Из золошлаковых отходов Ангарской ТЭЦ можно получать железный концентрат, подходящий по характеристикам для использования в качестве сырья металлургической промышленности, глинозем – сырье для алюминиевой промышленности, а также кремнезем и редкие металлы – скандий, лантан, иттрий, иттербий.
- Из лежалых хвостов ОФ Хинганолово, содержащих порядка 0,14 % олова, в черновой гравитационный концентрат извлекается не менее 80 % олова. Товарный концентрат в количестве 1600 т/год после флотационной доводки содержит не менее 65 % олова при суммарном содержании мышьяка, цинка и серы не более 0,5% [7].
К сожалению, широкомасштабное вовлечение в переработку техногенного минерального сырья сдерживается следующими факторами:
- Текущей законодательной базой РФ, которая рассматривает техногенные минеральные образования не как отходы производства, а как месторождения, и для их отработки требует геологического изучения, защиты запасов, а также соответствующего оформления и согласования в Министерстве природных ресурсов и экологии Российской Федерации.
- Отсутствие методологии расчета налога на добычу полезных ископаемых (НДПИ), учитывающей комплексность и повышение эффективности переработки минерального сырья.
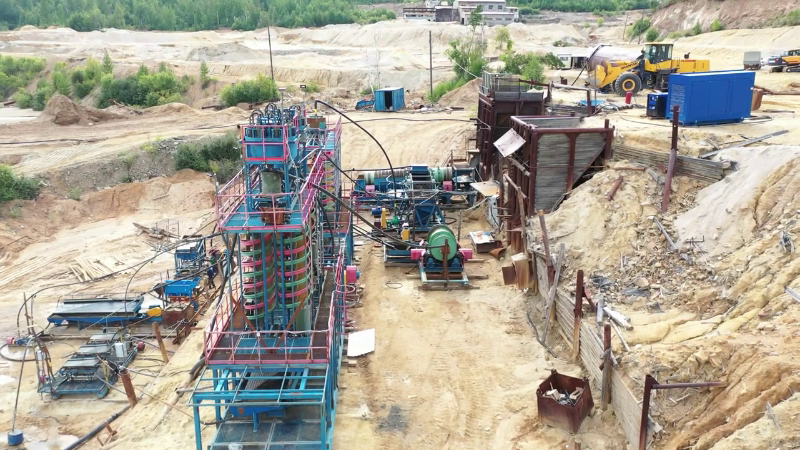
Однако, несмотря на проблемы и трудности, которые возникают при организации переработки техногенного минерального сырья, представленные выше примеры показывают, что переработка такого материала возможна уже сегодня, а в недалеком будущем это может стать экономически значимым источником металлов наравне с переработкой первичного минерального сырья.
Послесловие
Переработкой техногенного сырья наиболее выгодно заниматься в период существования у компании активов по переработке первичного сырья – руды и целиковых россыпей. Наличие таких активов предполагает присутствие необходимых технических специалистов, обслуживающего персонала, а также действующих объектов основной и вспомогательной инфраструктуры, необходимых для такой деятельности. Переработка ТМО по окончании сроков жизни предприятий потребует увеличение затрат как на обслуживающий персонал, так и на поддержание в рабочем состоянии объектов инфраструктуры.
Список использованной литературы
[1] https://www.finanz.ru/birzhevyye-tovary[2] https://kazakhaltyn.kz/about/us.html
[3] https://zolotodb.ru/article/12242
[4] https://allmineral.ru/stati/oczenka-effektivnosti-ispolzovaniya/
[5] https://www.polymetalinternational.com/upload/iblock/990/2021_01_29_Q4_Production_rus.pdf
[6] https://polyus.com/ru/investors/factsheet/
[7] https://www.khinganresources.com/
Автор статьи обладает опытом успешной реализации проектов по отработке техногенных месторождений от исследований до организации эксплуатации обогатительных установок. По вопросам проведения исследований, инжиниринга, разработке технологий и установок переработки техногенного сырья вы можете обратиться к автору статьи по телефону или электронной почте указанным на странице контакты.